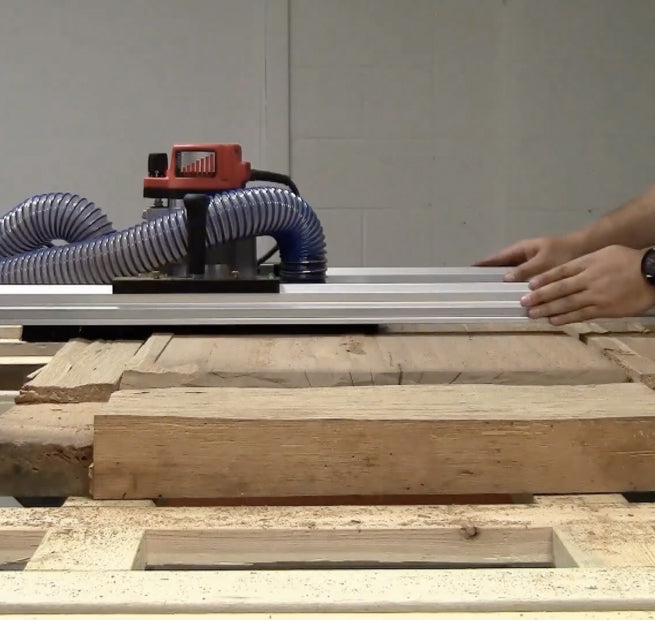
TrueTrac
Router Gantry System
Easily flattten large slabs, resin pours, traditional glue-ups, or any project too large for your planer or jointer.
Router Gantry System - The Ultimate Router Sled
Many router sleds are cobbled together from scrap materials or use unreliable components. The Router Gantry System takes a different approach. We learned from the limitations of those designs and engineered the RGS to be better from the very beginning. Effortlessly flatten slabs, expansive glue-ups, epoxy pours, and more with the TrueTrac Router Gantry System. This innovative system combines a versatile router sled and a powerful slab flattening mill, allowing you to tackle projects that wouldn't fit on a traditional planer or jointer. Shop now and unlock the potential for stunning woodworking creations!
Designed to be the most reliable router sled, it delivers smooth, level surfaces on large slabs and epoxy pours. Perfect for woodworkers tackling oversized projects that can’t be handled by standard tools, this slab flattening system is built to take your craftsmanship to the next level.

With your new Router Gantry System, you can reliably replace the functions of a traditional planer, jointer, and router table with a single tool, especially for large projects.
Setup or dismantling takes around 15 minutes total. The support table can be made in sections for easier storage, built against a wall and stored like a Murphy-style bed, or even lifted upwards to the ceiling when not in use via cables and a winch.
“Easy to assemble and I was very impressed with the quality of the machining." - Daimen B.

With the industry unique Threaded Cross-Feed upgrade you can pin your router down to a threaded rod that runs inside one of the bridge rails that create the width of the unit.
This allows you to accurately and repeatably control the width of your pass and make your cuts parallel to the grain of the lumber.
Have a gnarly piece with crazy grain patterns or a cookie? Consistent step-overs on each pass virtually eliminates tear out
“You Get What You Pay For - Excellent quality materials and construction. Heavy and solid and it’s clearly designed to last a lifetime or more.”
R. Irizarry
See what makes the RGS one of the best built router sleds available!
Arising from basic 2x6s and old bed frame rails, through units that rolled on caster wheels, or linear rods with recirculating ball bearings, the RGS was designed from the ground up to solve the problems found in those various designs.
Turn a week of hand planing into a project you actually get finished!
Watch this 77-second timelapse to see the RGS in action on 100+ year old oak.
We are using a 2-1/2 inch spoilboard bit with replacable carbide inserts on a 3-1/2 HP router.

With precision CNC-milled components the accuracy of the RGS unit will drastically reduce your finish sanding by up to 80%
Think 15-20 minutes, not 2+ hours
The Router Gantry System makes it simple to batch process smaller projects too, not just single large ones.
“...ready to conquer the 5ft wide 12+ft long slab we are going ro throw at it. Small/hometown build and all made in the USA... I will recommend to anyone that lays eyes on this rig!"
Bret Laitila (Arbor Custom Kilns) - Sept 10, 2022
FAQs - Router Gantry System
If you've got a question about our router gantry system that isn't answered here or among our videos, please don't hesitate to send us an email or give us a call!
A router gantry is a woodworking system that provides a stable and precise platform for routing operations over large surfaces. It consists of a framework that supports a router, allowing it to move along the X, Y, and sometimes Z axes with high accuracy.
A router sled is used for flattening large slabs of wood, creating even surfaces on uneven or rough lumber. It helps woodworkers achieve a smooth and level surface, essential for various woodworking projects.
For projects too large for your planer, jointer, or router table, a router sled can be an invaluable tool. With your new Router Gantry System, you can reliably replace the functions of these traditional tools, especially for large, irregularly shaped pieces
A router gantry system is more advanced and versatile compared to a basic router sled.
Key Differences:
Complexity and automation. Router sleds are simpler and manually operated, while gantry systems are more complex and can be automated. A router gantry system includes a gantry that allows the router to move along the X and Y axes over the workpiece. This system is often automated and controlled by computer software, providing higher precision and the ability to perform intricate woodworking tasks such as engraving, cutting, and shaping.
Precision. Gantry systems typically offer higher precision due to their controlled movements along multiple axes.
Applications. Router sleds are mainly used for flattening large slabs, while gantry systems are used for a variety of detailed woodworking tasks.
A manual feed system offers traditional, hands-on control, while a threaded cross feed system provides enhanced precision and consistency, reducing manual effort and expanding the range of possible operations.
The manual feed is basically "it goes where you push it" and you are in control of the router placement.
- This is the more ‘traditional’ router sled style of control where you’re basically emulating a rowing machine going back and forth across the width of the project to plane it down.
The threaded cross feed units have a threaded rod that you can pin the router to in order to control the placement across the width of the unit.
- This allows you to have consistent width passes parallel to the grain or long axis of the mill. This gives a much better surface finish (which means less sanding), plus none of us have 4ft long arms to reach across the entire width in one go.
- It also opens up the ability to handle inlays, edge jointing, equally spaced fluting, and other straight line routing operations since you can control the router's position with a simple hand crank.
- Effectively turns the unit into a router table flipped upside down.
It honestly depends on volume. We split it into two categories:
For 3 tables, slabs, or projects per month or less:
- Woodline USA part numbers 1394-1 and 1394-2
- -1 for roughing work, -2 for finishing work, both run around $40 per bit and are solid carbide two wing bits with a ½ inch shank.
As a perk those are made in Tennessee.
If you're planning on more than 3 slabs per month, it’s totally worth it to get the bits with the replaceable carbide inserts
- Amana RC2255, RC2263 or similar bits work great, though the initial purchase is up over $150 once that is taken care of the replacement inserts are ~$30/ea and have four cutting surfaces to rotate through
Generally, we stay with 2-1/2 inch diameter bits or less, though most of the 3+ HP routers can swing a 3-1/2 bit with proper precautions and experience.
Start smaller and get comfortable with the RGS before jumping into that size bit.
If you’re doing smaller projects in the cutting board to coffee table sized arena, you can stick with the 2-1/2 HP routers
- In particular we’ve had solid luck with the Bosch 1617-EVS (fixed base) and it’s probably the industry leader in the 2 HP category.
For larger projects you’ll need a larger router, but not for the reason you’re likely thinking.
- Larger 3+ HP routers are designed for longer duty cycles and have fans that move significantly more air through the motor, so longer run times do not build up the same amount of heat. Heat is what will kill the smaller router motors faster than anything.
- Yes, you can also swing larger bits with a larger router which means you’ll spend less time overall planing down your projects, but longevity is really the biggest reason to jump into the larger routers.
- The Milwaukee 5625-20 is our go-to for the 3HP range, as it has one of the nicer depth adjustments on the market for that size router. Bora, Triton, DeWalt, Makita, and JessEm also make fantastic router motors in the same HP range.
Plunge style routers are nice for projects where you need to make a cut, lift the router to reposition, and then return to the same depth of cut without counting turns or anything of that nature.
- Equally spaced flutes, box border inlays, tenons at opposite ends of the projects, etc.
A fixed base router with a nice depth adjustment is about as simple as it gets, so if you’re just looking to plane out and process slabs or table glue-ups it’s hard to beat.
- Slip-It sliding compound (silicone free version) is what we’ve been utilizing most recently with excellent results. It’s effectively a synthetic paste wax that doesn’t seem to attract dust and lasts a fair amount of time.
- Apply to both the linear slides and the aluminum rails themselves with a rag and wipe off any significant excess with
- Alternatives are normal paste wax like Johnson’s or Minwax
Spray-on dry film lubricants like white lithium, molybdenum disulfide, graphite, or other lubricants like bearing grease really aren’t what you should use. You can, it isn’t going to hurt anything material-wise, but it won’t be effective.
- We prefer not to do custom sizes, mostly because there’s no real need to. We bring the extrusions in already cut-to-length in 55-inch sections. We then cut and match 27-1/2-inch sections for shorter extensions.
- If a custom size extension is required, we can cut them to the desired length of 55 inches or less, but the pricing will remain the same as we’ll just end up with a weird length scrap off-cut. Contact us via email with the sizing requests.
- Standard extensions legitimately add either 55 or 27-1/2 inches of capacity, as the ‘dead space’ is already accounted for within the base kit sizes.
- If the bottom long axis rails are on the same surface as the material being cut, the RGS unit is rated for 2-1/4 material (9/4 boards)
- You can increase this capacity by raising the bottom long axis rails relative to the
support surface. For instance, making the banding boards from 2x6 material rather than 2x4 material will raise that capacity by 1-1/2 inches, giving you a 3-1/2 to 3-3/4 inch thickness capacity. - Alternatively, the table can be designed with a lift system that the long axis rails are
affixed to such that the rails can be lifted upwards and pinned in various positions. - If need be you can also construct pylons for the RGS to rest upon in the case of needing to plane out projects that are already installed or in place such as a bar top. Simply create pylons down to the flooring and build the RGS unit above or around the item being planed. This could include large stumps or burls.
All units are named for the closest nominal effective working area that the unit creates.
- A 48x48 unit can legitimately plane down a 48x48 inch slab
- A 48x96 unit can legitimately plane down a 48x96 inch slab, with the length capacity being undersold since it can handle 102 inches of material.
- A 22x96 and a 48x72 unit are identical in component make-up, the only thing that changes are how the rails are arranged.
All rails are the same design; therefore, you can expand both the length of the units as well as the width of the units
- 72 inches wide is the widest capacity unit we will sell. This is made by joining a 55-inch rail to a 27-1/2-inch rail for a total rail length of 82-1/2 inches, which is honestly a massive span. See notes below regarding deflection.